En 2020, le distributeur et fabricant d'équipements sportifs Decathlon avait tenté l'aventure de la conception générative pour développer une fourche de vélo de course. Pour cela, il a exploité la plateforme collaborative Design & Make, basée sur la CAO Autodesk Fusion 360. Le résultat satisfaisant a poussé le Nordiste à renouveler l'expérience, cette fois avec la refonte complète d'un produit, en l'occurrence des palmes de plongée.
L'entreprise a souhaité repartir d'une page blanche en oubliant les habitudes de conception appliquées jusque-là, pour disposer d'un produit à la fois plus efficace et plus confortable pour des plongeurs expérimentés. En se positionnant volontairement en rupture avec les modèles traditionnels, Decathlon voulait, par exemple, maintenir une rigidité constante tout au long de la palme, plutôt que de la réduire depuis le talon jusqu'au bout de la voilure. Les palmes devaient aussi être faciles à enfiler dans l'eau et à transporter, et supporter une utilisation fréquente. À la faveur de ce nouveau départ, Decathlon a aussi voulu réduire l'empreinte environnementale de ce produit, en utilisant des matières premières plus adaptées et recyclables, en réduisant la quantité de matière première plastique (procédé de fabrication par injection) et en s'assurant qu'elles seraient recyclables.
Une forme organique proposée par l'IA
Résultat, à partir de ces nombreuses exigences, l'algorithme a rapidement proposé de multiples solutions, dont une forme atypique, résistante et rapide, mais néanmoins confortable et au coût environnemental réduit. « La forme de la palme se démarque par sa structure organique et sa finesse semblable à une feuille déformée, complète Raphaël Vis, chef de projet circularité et designer chez Decathlon. Mais il s'agit aussi d'une palme ultra légère et compacte avec un comportement réactif dans l'eau. »
Armand Macé, ingénieur produit chez Decathlon, ajoute, dans une vidéo sur le site de l'entreprise : « nous voulions simplifier la relation entre le maintien du pied et la poussée dans l'eau. D'où l'idée d'une épaisseur constante, de ne pas remplir la partie près du pied où il y a habituellement beaucoup de matière, mais de travailler la forme à la façon d'une tôle ondulée pour donner de la rigidité. Finalement, on obtient une palme qui va se déformer dans l'eau. » L'équipe a demandé au logiciel des niveaux de déformation de la voilure par exemple, avec un certain degré de force. La conception générative a proposé d'intégrer des structures entre l'extrémité de la voilure et le chausson avec des formes plus ou moins inattendues, organiques.
Economiser la matière première et assurer la recyclabilité
Le generative design s'appuie, en effet, sur des algorithmes de machine learning pour imaginer différentes alternatives de conception à partir de nombreux paramètres. À l'instar des jumeaux numériques d'infrastructures complexes, les designs génératifs accueillent un très grand nombre de paramètres pour générer en sortie, en quelques minutes, un grand nombre de designs, tout en restant en mesure d'adapter les paramètres de départ pour affiner le résultat. La solution de generative design se base sur des algorithmes alimentés, entre autres, avec des données sur les développements cellulaires, génétiques et osseux.
Il en est allé de même avec les exigences de réduction de l'empreinte environnementale. Les nouvelles palmes utilisent 50% de matière en moins que les modèles standards du marché, elles sont fabriquées avec de la matière recyclée et sont recyclables en fin de vie. La voilure est en plastique recyclé, mais la palme est fabriquée en monomatière pour faciliter un recyclage sans démantèlement. « Le design final permet par ailleurs d'utiliser une structure en thermoplastique dur afin de réduire l'usage des élastomères dont l'impact en CO2 est plus important », précise Raphaël Vis.
Ce dernier explique, par ailleurs, que ce projet qui pourrait en inspirer d'autres a aussi modifié le processus de conception et l'organisation associée. « La nouveauté, c'est que nous avons intégré des boucles itératives 100% digitales avant de basculer vers les premières phases de prototypage et les tests physiques. Nous avons généré, puis testé plusieurs architectures que nous avons comparées en simulant la déformation et en analysant l'effort de poussée dans l'eau en digital. »
Avec la GenAI, Decathlon conçoit ses futures palmes
0
Réaction
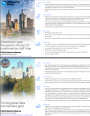
Après un premier tour avec la conception générative pour le design de la fourche d'un vélo de course, Decathlon replonge. Cette fois pour repenser totalement, à partir d'une page blanche, une paire de palmes légères, rapides, à l'empreinte environnementale divisée par deux.
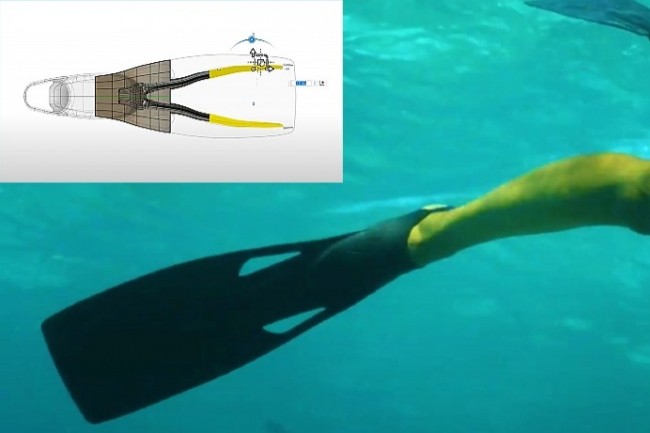
Newsletter LMI
Recevez notre newsletter comme plus de 50000 abonnés
Commentaire