Un paquebot de plus de 600 mètres de long posé sur l'ancien site de la Française de mécanique, à cheval sur les communes de Billy-Berclau et Douvrin, entre Lens et Lille. La première Gigafactory de France s'apparente encore à une ruche. Près d'un millier d'ouvriers - dont de très nombreux Coréens et Chinois qui livrent l'essentiel des machines au coeur du processus industriel complexe de production des batteries -, s'affairent encore à la finalisation de l'usine qui doit livrer ses premiers modules de batteries à Stellantis en novembre prochain. Un calendrier contraint qui pousse ACC (Automotive Cells Company), l'industriel qui porte ce projet et qui est soutenu par l'État et des actionnaires majeurs (TotalEnergies, Stellantis et Mercedes-Benz), à commencer la prise en main du futur appareil de production. Les 300 premiers salariés de l'usine de Billy-Berclau Douvrin (ou BBD) sont déjà à pied d'oeuvre. Le site est appelé à atteindre les 1200 salariés en 2025, selon les plans d'ACC.
Côté informatique, François Carrot, le DSI, doit faire face à des contraintes similaires : livrer rapidement un système d'information minimal, tout en construisant celui de demain, quand l'entreprise comptera 3 gigafactories (Billy-Berclau-Douvrin, Kaiserslautern en Allemagne et Termoli, en Italie) et emploiera plus de 10 000 personnes. « Nous sommes partis d'une page blanche, mais en voyant grand », dit le DSI, recruté en novembre 2020 après une carrière d'une trentaine d'années dans l'automobile. Un des enjeux consiste à accompagner le passage à l'échelle du jeune industriel - ACC est né début 2020 -, avec d'abord la naissance en 2021 du centre de R&D de Bruges (à côté de Bordeaux), d'où sont sortis les premiers modules, puis la création de l'usine pilote de Nersac, en 2022. Et, désormais, Billy-Berclau-Douvrin, sur une échelle qui est tout autre. Le premier bloc en cours de finalisation - l'usine doit en posséder 3 à terme - affiche une capacité de production de 13,4 GWh en 24/7, 365 jours par an. De quoi équiper 100 000 à 200 000 véhicules !
« Aucun modèle à répliquer »
« Sur le plan IT, partir d'une page blanche est évidemment une chance unique, reprend le DSI. Sauf qu'il n'existait aucun modèle que nous aurions pu répliquer. Et il fallait construire le système d'information très vite pour répondre aux besoins essentiels d'ACC, et surtout le construire en même temps que se construisait l'entreprise, son centre de R&D, son organisation, ses usines ». Si le département IT peut un temps s'appuyer sur les actionnaires de la société pour certaines fonctions transverses (comptabilité et paye), l'essentiel de sa feuille de route découle des attentes du Pdg, Yann Vincent.
François Carrot, le DSI d'ACC (à gauche) et Lionel Taisne, le responsable IT de la gigafactory de Billy-Berclau-Douvrin. Derrière eux, l'allée principale de l'usine, mesurant plus de 600 mètres de long. (Photo R.F.)
En tête de liste, la volonté de rattraper le retard pris sur les industriels asiatiques. « D'où une exigence de performances, de maîtrise des coûts de revient et de réduction des rebuts, en particulier le taux de modules de qualité insuffisante (en jargon, le scrap, NDLR) qui doivent être recyclés. D'emblée, il nous a demandé d'exploiter la data au maximum pour maîtriser ces paramètres », reprend François Carrot. ACC a traduit son ambition sur les datas en créant une entité dédiée à la valorisation de la data, entité dirigée par un CDO (Chief Data Officier).
Pour le démarrage de la production, ACC prévoit de mesurer la qualité à chaque étape d'un processus de fabrication qui en compte neuf. « Si nous ne rentrons pas dans le détail, nous ne progresserons pas sur le rebut (le taux de cellules défaillantes, NDLR) », dit le DSI. (Photo : ACC)
Autre élément clef pointé par le dirigeant, et très sensible dans les choix effectués par François Carrot et ses équipes : la cybersécurité. En particulier la capacité à protéger l'appareil de production des menaces externes. « Parce que c'est un des moyens les plus simples de nous faire prendre du retard dans la compétition mondiale qui s'amorce ! », pointe le DSI. Pour l'instant, au sein de la gigafactory BBD encore en chantier, les machines restent la propriété de leurs fabricants asiatiques. « Dès que le transfert de propriété sera acté, nous mènerons un audit de sécurité pour traquer les éventuelles failles et autres accès à distances », détaille Lionel Taisne, le responsable informatique de la première usine ACC.
Traçabilité : au niveau de l'agroalimentaire et de la pharmacie
Le Pdg imprime encore deux autres priorités sur la feuille de route de la DSI : le respect de la politique RSE du groupe - sans oublier la contribution de l'IT à la maîtrise des émissions de l'entreprise - et la traçabilité sur toute la chaîne de fabrication, en raison de la dangerosité des produits manipulés. « Les exigences en matière de responsabilité sociale et environnementale sont essentielles. À partir de chaque cellule en bout de chaîne, il faut être en mesure de remonter au feuillard (une feuille d'aluminium ou de cuivre où sont enduites les encres, NDLR) et aux matières premières, le lithium et le manganèse. Ce lien de généalogie est au niveau de ce qu'on trouve dans l'agroalimentaire ou la pharmacie », indique le DSI.
Ces gigantesques armoires, installées en bout de chaîne, servent à tester les cellules, via des cycles de charge et décharge. ACC entend utiliser le machine learning pour pronostiquer la courbe de décharge et ainsi écouter ce processus qui s'étale sur plusieurs jours. (Photo : R.F.)
Cette feuille de route exigeante, couplée au calendrier serré de montée en charge de l'activité, pousse la DSI à travailler avec une double focale. « Il faut à la fois livrer à court terme des systèmes, car les attentes sont fortes, tout en nous préparant à répondre aux ambitions affichées à deux ou trois ans », résume François Carrot. Aujourd'hui composée d'une quarantaine de personnes au niveau central (des équipes informatiques sont aussi déployées dans les usines, qui conservent une forte autonomie en matière d'IT, voir encadré), l'IT d'ACC est décomposée en six groupes, reflétant les problématiques essentielles auxquelles l'entreprise fait face : infrastructures et cybersécurité ; ERP ; ingénierie, industrialisation et qualité (autour du PLM essentiellement) ; fonctions transverses (comme les RH) ; gestion de la donnée ; et, enfin, manufacturing, autour du MES (où Aveva de Schneider Electric a été retenu). « Notre méthode de travail consiste à travailler délibérément en silos, avec peu d'interfaces, pour que chacun puisse avancer à son propre rythme, détaille le DSI. Mais nous avons veillé à définir nos données de référence pour créer des interfaces dans un second temps. »
Maîtrise de la logistique : avancer étape par étape
Pour avancer rapidement, François Carrot a émis ce qu'il présente - avec le sourire - comme un oukase : « ne prendre que des systèmes sur étagère, sans développement spécifique ». Exemple emblématique de cette volonté de rester dans le standard pour aller vite : l'implémentation de l'ERP QAD en quatre mois, pour la finance et les achats indirects. D'abord installé on-premise, le progiciel a depuis migré sur un cloud, pour accompagner la stratégie de l'éditeur. « À notre demande, cet environnement a été installé chez OVH, au lieu d'IBM qui est l'hébergeur habituel de QAD », précise François Carrot. L'ERP a également été étendu à la logistique et aux achats directs, un enjeu majeur étant donné le coût des flux de matières que manipulera ACC. « Nous avancerons par étapes. Pour l'instant, ces processus sont supportés par notre ERP. Mais, quand il faudra aller plus loin sur la gestion des transports ou les prévisions - dès 2024 -, nous envisagerons des systèmes complémentaires », dit le DSI.
Sur le flanc du premier bâtiment de la gigafactory, d'anciens bâtiments de la Française de Mécanique ont été rasés et le terrain terrassé. C'est ici que sera construite la seconde tranche, attendue pour fin 2025 ou début 2026. (Photo : R.F.)
Pour ce dernier, un autre sujet embarque encore davantage de complexité : le MES. « Car nous devons construire le système tout en améliorant notre maîtrise des process de fabrication ». Le spécialiste interne du sujet vient tout juste d'être recruté. Cette question de la maîtrise du processus industriel est également central dans l'exploitation de la donnée : là aussi, la DSI doit récupérer les données issues de ses processus de fabrication tout en livrant les premières analyses, essentielles à la maîtrise de la qualité. Le centre de R&D ainsi que l'usine pilote de Nersac ont permis de récolter de premiers jeux de données issus des équipements. « Notre équipe data s'en est servi pour bâtir de premières applications portant sur la généalogie des produits et proposer de premiers tableaux de bord. Une app pour tablette a également été développée pour que les opérateurs puissent saisir des informations », relève le DSI. « Pour la récupération des données des machines, nous avons appris au fil de l'eau », abonde Lionel Taisne.
La donnée à l'échelle d'une gigafactory
Mais la gigafactory des Hauts-de-France place la barre encore bien plus haut. Tant en matière d'échelle (par exemple, une seule machine d'empilage est présente dans l'usine pilote, là où 46 seront déployées à BBD !), qu'en matière de diversité des équipements déployés. « Nous faisons face à un travail important de maîtrise des données. Chaque équipementier peut nous fournir un certain nombre de variables. En dehors du fait que celles-ci ne sont pas forcément traduites depuis le Chinois ou le Coréen, il faut déterminer à quoi elles correspondent et leur utilité réelle », résume Lionel Taisne. Les équipes d'ACC sont donc en train de construire des tables d'échange entre les formats sources et les formats cibles, tables que l'industriel prévoit d'intégrer à ses futurs appels d'offres, qui seront lancés pour ce que la société appelle sa Wave 2 (soit la seconde tranche de BBD, la première de Kaiserslautern et deux tranches à Termoli). « Pour l'instant, nous sommes encore très loin du monde rêvé de l'OPC UA* plug & play », glisse François Carrot.
* : OPC UA (Open Connectivity - Unified Architecture) est un standard d'échange de données facilitant l'interopérabilité des systèmes industriels. La norme est maintenue par la fondation OPC, consortium industriel spécialisé sur les standards de l'automatisation.
Les coulisses de la création du SI de la Gigafactory d'ACC
1
Réaction
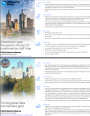
Dans les Hauts de France, la première gigafactory française de batteries pour l'automobile est sortie de terre. Pour supporter cette activité nouvelle, la DSI d'ACC, l'industriel à la tête de ce projet a bâti un système d'information en un temps record. Reportage.
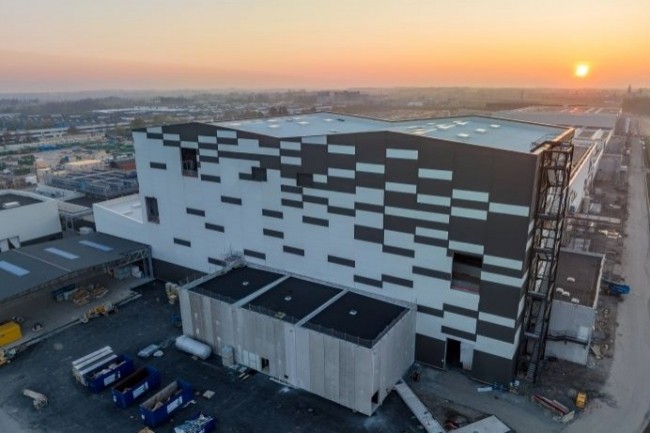
Newsletter LMI
Recevez notre newsletter comme plus de 50000 abonnés
Je vois un SPF (single point of failure) dans cette description: l'ERP hébergé chez OVH.
Signaler un abusQuel est l'intérêt de ce choix ?