Le groupe de chimie Dow récolte les fruits d'un programme lancé il y a un an en vue du déploiement de nouvelles technologies numériques sur l'un de ses plus grands sites de production, puisqu'il lui a permis d'améliorer les performances, la fiabilité et l'expérience des employés. Voilà plus de cinq ans que Dow Chemical a fusionné avec DuPont pour former DowDuPont - et trois ans que les deux entités se sont à nouveau séparées pour donner naissance à une entreprise de fournitures agricoles, Corteva ; un fabricant de produits chimiques spécialisés, Dupont, et un fournisseur de produits chimiques courant, Dow. « C'est l'une des plus grandes scissions que je connaisse, et l'un des projets les plus complexes sur lesquels j'ai travaillé », confie Melanie Kalmar, qui a été la DSI de Dow pendant toute cette période. « En tant que nouvelle entreprise, Dow se devait aussi d'être plus numérique, mais pas pour le plaisir », ajoute-t-elle. « Il fallait changer la façon de travailler des employés, pour qu'ils soient plus efficaces, plus efficients et stimuler la croissance de l'entreprise en se concentrant sur des activités à plus forte valeur ajoutée », explique la DSI.
Premier effet positif de cette approche : la mise en place d'un programme visant à sortir l'informatique du bureau et à accélérer le déploiement des technologies numériques dans les secteurs de la fabrication et de la maintenance. Ce projet a même valu à Dow un prix CIO 100 pour son innovation et son leadership en matière d'IT. L'objectif était d'améliorer la productivité, la sécurité et la fiabilité des « actifs » de fabrication - le terme utilisé par Dow pour désigner les vastes étendues de béton et d'acier et les réseaux extérieurs tentaculaires de tuyaux et de commandes qui caractérisent ses installations de production. « Tout repose sur notre volonté d'être le fournisseur le plus fiable du secteur », souligne Mme Kalmar. C'était un vrai enjeu pour les clients de Dow après les deux années de confinements, de pénurie de main-d'oeuvre, d'événements climatiques extrêmes et autres perturbations de la chaîne d'approvisionnement qu'ils avaient dû affronter.
Montrer le ROI sur un site de grande envergure
Plutôt que de commencer par un petit site pilote, la DSI et ses collègues ont opté pour un projet de grande envergure, en choisissant pour leur premier déploiement le plus grand site de production de Dow à Freeport, Texas, qui s'étend sur 2 000 hectares. « Nous voulions montrer le retour sur investissement que pouvait générer un tel projet, et forcément, avec un site plus petit, le retour sur investissement aurait été moindre », note Mme Kalmar. « Sur un site comme Freeport, la plupart des employés se trouvent dans la salle de contrôle, où ils surveillent les vannes qui s'ouvrent et se ferment à partir d'un tableau de bord », poursuit la DSI. Auparavant, s'ils devaient sortir pour effectuer une maintenance ou une série de contrôles physiques, ils devaient faire des allers-retours entre les actifs et la salle de contrôle pour récupérer les ordres de travail ou imprimer la documentation. Désormais, ils accèdent à ces informations dans un cloud sécurisé, via un appareil renforcé en matière de sécurité et connecté à un réseau sans fil 4G privé à l'échelle du site. « Nous avons mis toutes ces informations dans leur poche, sur ces appareils mobiles », ajoute Melanie Kalmar. « La rapidité avec laquelle ils peuvent entretenir, corriger ou réparer quelque chose à l'extérieur de l'usine a un impact énorme sur la fiabilité globale », fait observer la DSI.
« Les employés sont également ravis d'avoir ce dont ils ont besoin avec eux immédiatement et de ne pas avoir à imprimer du papier, surtout s'il pleut ou s'il y a du vent et que les papiers s'envolent », pointe Mme Kalmar. Les informaticiens qui ont déjà eu du mal à faire passer des câbles Ethernet dans les gaines d'un bureau ou même d'une petite usine comprendront l'intérêt du sans-fil sur un site de la taille de Freeport, mais la DSI affirme que cette technologie présente aussi ses propres défis : « Sur un site de production, il ne suffit pas d'aller avec une pelleteuse et de creuser n'importe où pour installer un poteau. Toute cette planification et cette exécution étaient très nouvelles pour mon équipe », souligne Mélanie Kalmar.
Une collaboration mûrement préparée
« Ce serait difficile de faire ce genre de chose dans des entreprises où les services IT et OT ne travaillent pas ensemble, mais ce n'est pas le cas chez Dow », indique Melanie Kalmar. « L'une des premières actions après mon arrivée chez Dow a été de m'associer avec le vice-président de la fabrication. Nous étions d'accord sur le fait que nous pourrions faire mieux pour l'entreprise si nos équipes collaboraient », affirme la DSI. « Surtout, nous étions d'accord sur le fait que l'objectif n'était pas d'acquérir les compétences des uns et des autres, mais plutôt de les exploiter : collaborer, tout en laissant certaines tâches aux experts », poursuit-elle. « Nous avons suivi toutes les étapes préconisées par la méthode de gestion de projet RACI (Responsible, Accountable, Consulted, Informed) et nous avons identifié qui était responsable et redevable de ce qui se passe avec la technologie sur nos sites, à tous les niveaux. Grâce à cette collaboration, nous avons établi un partenariat beaucoup plus solide sur ce sujet, et nous envisageons même des plans de carrière transverses entre les deux entités ».
Il existe déjà chez Dow, dans d'autres domaines spécialisés, des plans de carrière couvrant plusieurs départements, dans la science des données notamment, où les experts peuvent être amenés à travailler dans l'IT, la fabrication, la R&D ou la gestion de la chaîne d'approvisionnement. « Il suffit de se lancer et de commencer à briser les silos historiquement et traditionnellement présents dans les entreprises », suggère la DSI. « Si l'on cherche par tous les moyens à améliorer l'expérience des clients et des employés, des opportunités finissent vraiment par émerger. Et elles ont changé l'état d'esprit chez Dow ». Mais il y a encore des limites. « Par exemple, le secteur de la fabrication est toujours responsable des systèmes de contrôle qui dirigent les équipements de fabrication, même si l'IT commence à s'impliquer davantage dans le réseau sur lequel ces systèmes de contrôle fonctionnent », observe Melanie Kalmar.
Il a également fallu renforcer l'organisation de l'IT pour le projet, en ajoutant des compétences en matière de cloud, de réseaux et de sécurité. Cependant, c'est dans la gestion du changement que le besoin de compétences était le plus important. De fait, Mme Kalmar a étoffé son équipe de direction en recrutant une personne spécifiquement chargée d'accompagner le changement dans l'entreprise, notamment en identifiant les personnes à intégrer en priorité afin de favoriser l'adoption des nouveaux systèmes, pour ne pas se contenter d'offrir une formation à ces systèmes. « Dans une entreprise où la production tourne en permanence, qui a le temps pour consommer et accepter un nouveau système qui vient de sortir ? », observe Mme Kalmar. « Nous envisageons le changement de manière très différente ».
Prêts à passer à la 5G
Pour l'instant, le réseau sans fil privé de Dow utilise la 4G/LTE, mais il sera prêt pour la 5G quand la technologie elle-même sera prête. « Tout le monde s'emballe pour les réseaux 5G, mais il faut avoir des appareils et des applications compatibles. Nous allons donc attendre un peu pour sauter le pas, mais nous serons prêts à faire ce changement. L'infrastructure que nous avons mise en place pourra basculer en 5G », indique la DSI. L'usage d'une technologie sans fil plus ancienne et plus lente n'a cependant pas nui au projet, au contraire. Selon Dow, plus de 3 600 employés ont été formés aux nouveaux outils, si bien qu'ils peuvent effectuer en moins d'une minute des tâches liées aux données, au lieu d'une demi-heure ou plus auparavant. Selon Mme Kalmar, lors du déploiement sur un site géant comme celui de Freeport, il est important de reconnaître dès le début que des solutions uniques ne fonctionnent pas toujours, et de passer du temps en amont à discuter avec les collègues et à obtenir les bonnes informations. « Il faut ajuster son approche traditionnelle du programme et être ouvert à des mises en oeuvre pilotes à grande échelle », recommande-t-elle. « Il est aussi important d'apprendre à mesure que l'on fait, de communiquer sur ses succès et de rester à l'écoute des parties prenantes », conclut-elle.
Le géant de la chimie Dow fait collaborer IT et OT
1
Réaction
En favorisant la coopération entre les équipes technologiques et opérationnelles, le géant de la chimie Dow a pu mieux exploiter les nouvelles technologies de communication sur l'un de ses plus grands sites de production.
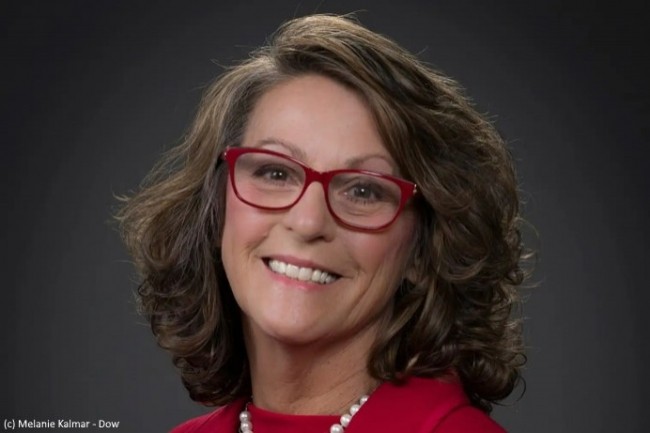
Newsletter LMI
Recevez notre newsletter comme plus de 50000 abonnés
Je lis : "Il fallait changer la façon de travailler des employés, pour qu'ils soient plus efficaces, plus efficients" C'est quoi la difference entre des employés plus efficaces et des employés plus efficients ?
Signaler un abus